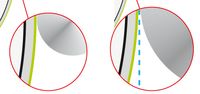
Why larger metering bar diameters increase production disproportionately
Generally, 10 to 15 mm diameter metering rods with smooth surface are applied in direct coating, or with profiled surface in the filmpress.
Depending on the content of abrasive components in the coating media, a service life of two to four weeks can be reached. This practice applies to paper machines operating 24/7 throughout the world. However, since it prevents innovative advantages, the motto "Never change a running system" is counter-productive in an increasingly tougher competition.
When each additional production hour and waste minimization count, metering rods must offer a longer service life and less frequent revision cycles. A simple technological solution is the use of metering rods with a larger diameter, allowing above average run times.
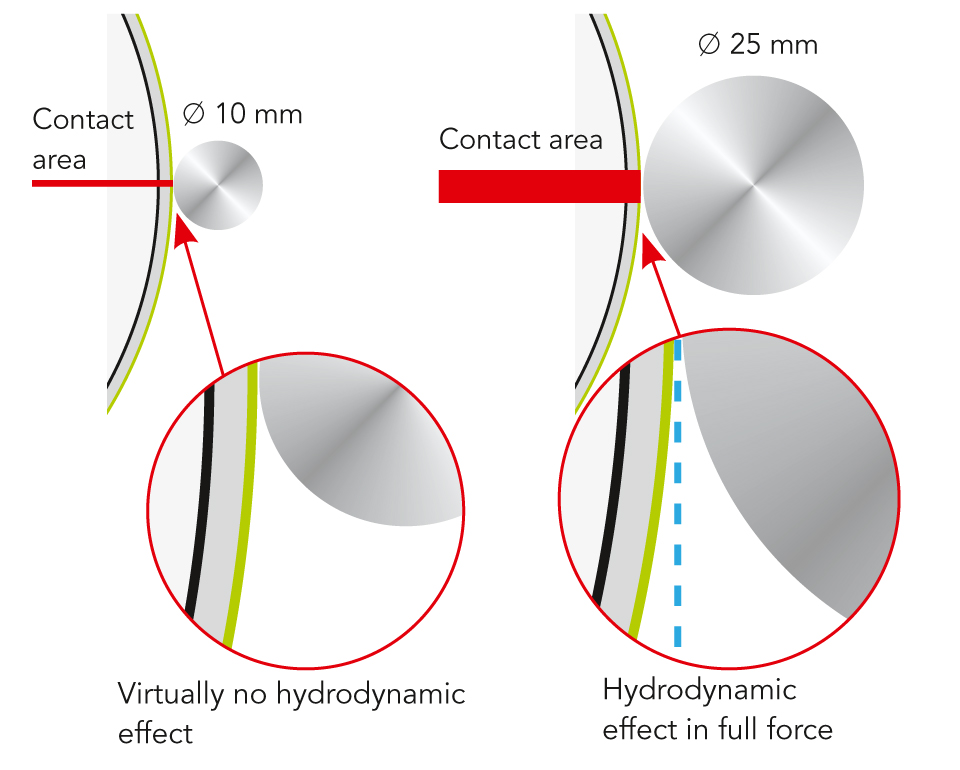

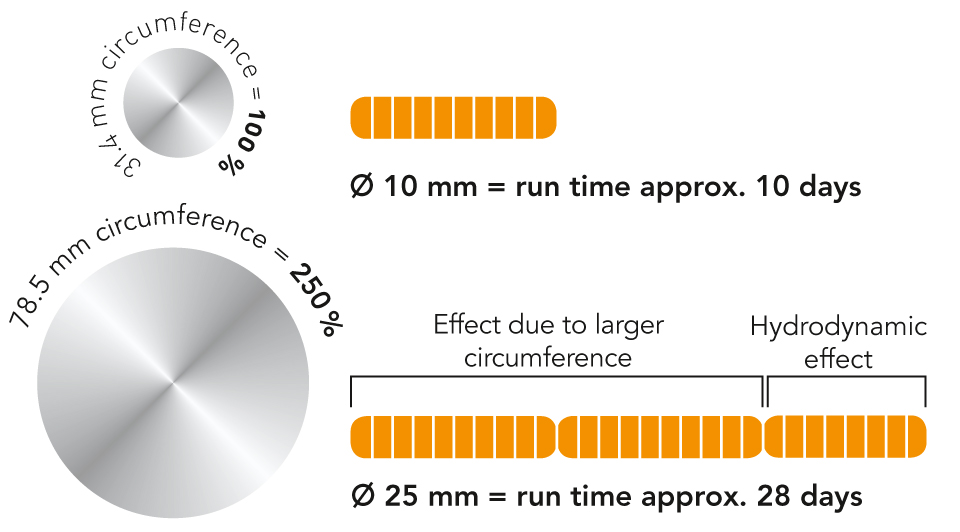

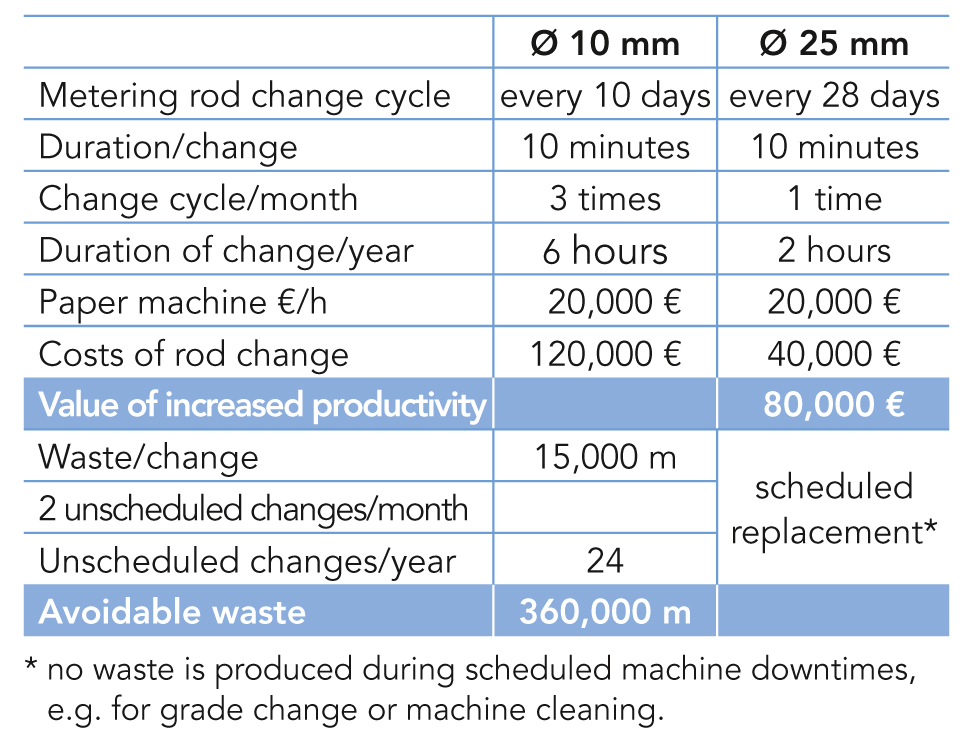

- The forces responsible for wear act on a larger area; for this reason, the rods withstand load for a longer period.
- The linear load of the metering rod against the sheet or backing roll is uniform and
- gentle. The result: lower pressure, no"penetration" of the rod, less deformation, and longer service life of backing roll cover.
- Hydrodynamic processes minimize the direct contact between metering rod and sheet, similar to aquaplaning when driving: A thin water film between tires and road virtually reduces the tire wear to zero. The same applies to the contact between metering rod and paper.
Whereas the first two effects have proportional impacts on the service life of the metering rods, the hydrodynamic effects ensure a significant above average extension of run time.
Secondary advantage: Metering rods with large diameter are clearly more resistant to sheet break, out-of-center drives, and improper handling.
Larger metering rods = higher productivity
Sample calculation based on the following assumption:
Product: Paper, wood free
Machine speed: 1500 m/min
Coat: 3g/m² total
Coating: Surface sizing
Metering rods: Profiled geometry